Personal Care
Wype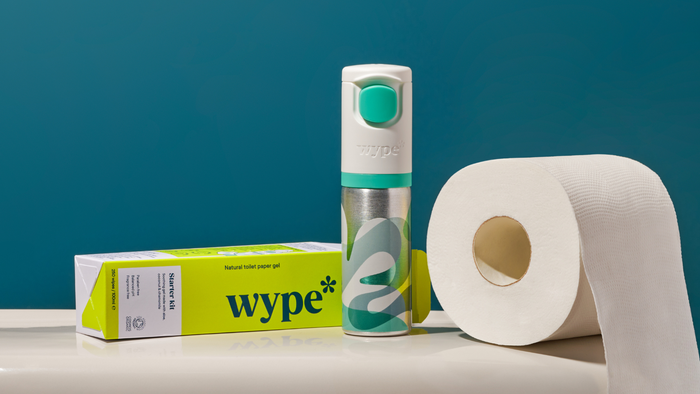
Personal Care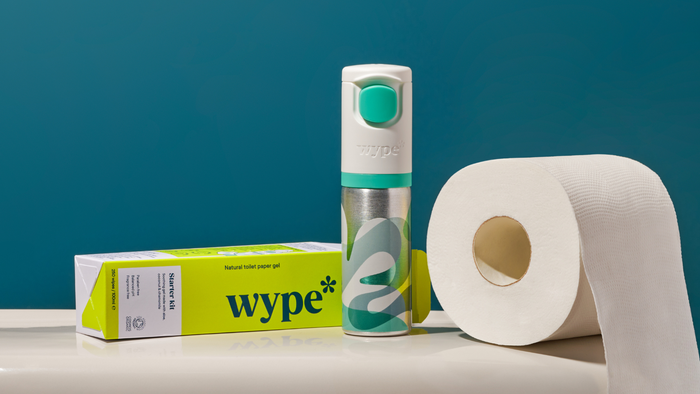
Wype reimagines the future of bottom careWype reimagines the future of bottom care
Eco-friendly organic gel displaces wet wipes for a better clean without the extra waste. No butts about it.
Subscribe and receive the latest updates on trends, data, events and more.
Join 57,000+ members of the natural products community.