thumbnail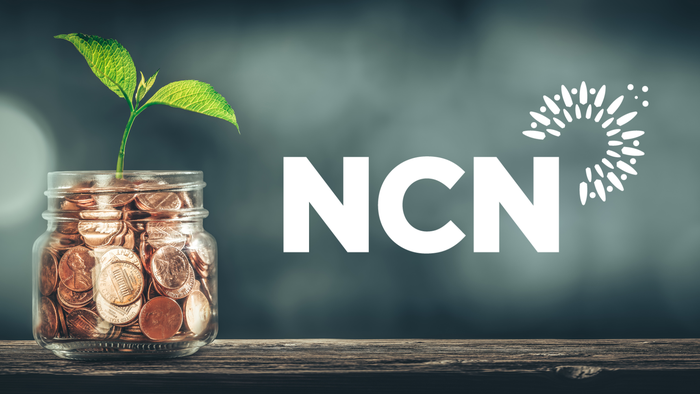
Investments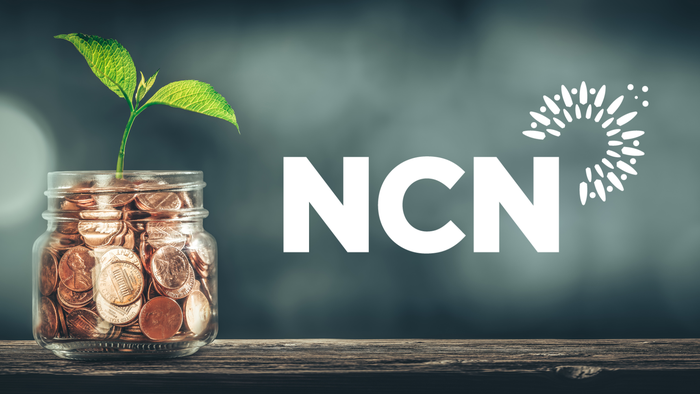
3 not-to-miss sessions at NCN spring 20243 not-to-miss sessions at NCN spring 2024
The annual NCN Spring Investor Meeting dives deep into the investment side of the natural and organic products industry, with panel discussions, networking and much more.
Subscribe and receive the latest updates on trends, data, events and more.
Join 57,000+ members of the natural products community.