Market Data and Analysis
thumbnail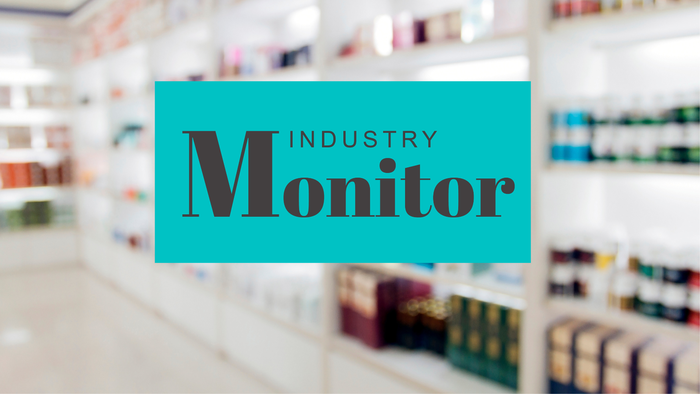
Market Data and Analysis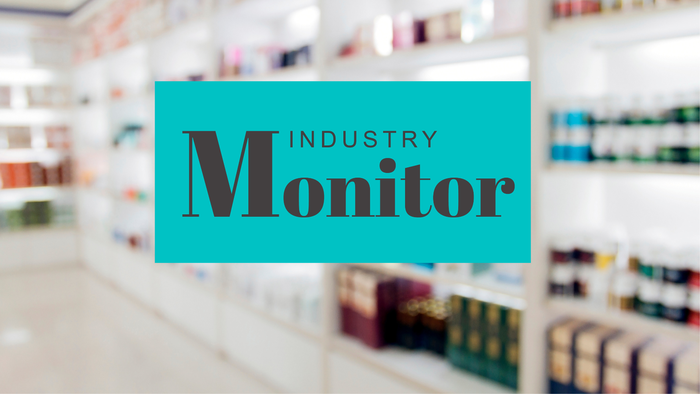
Monitor: Consumer trust in supplements grew after pandemicPandemic bolstered trust in supplements
New consumer research shows that trust in supplements grew post-pandemic, even after sales growth fell in wake of the "COVID boom."
Subscribe and receive the latest updates on trends, data, events and more.
Join 57,000+ members of the natural products community.