The final frontier
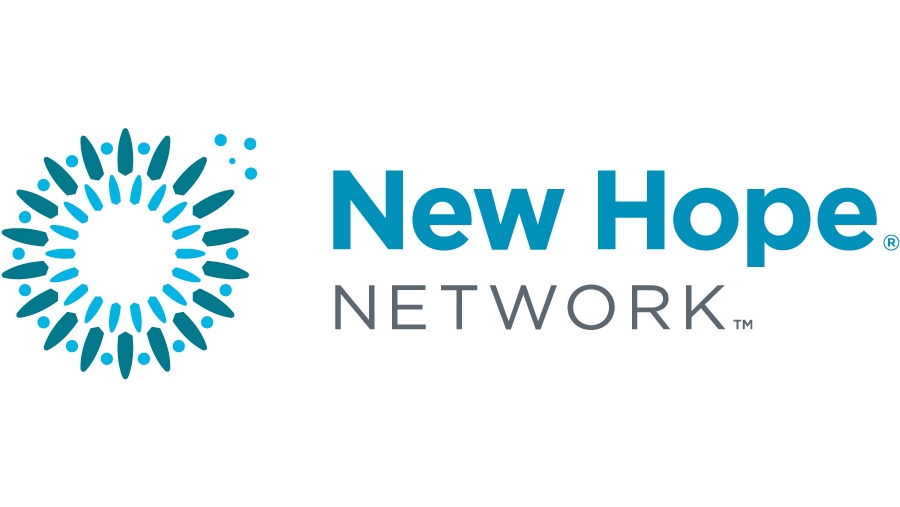
D-day is approaching for the final round of GMP compliance. Functional Ingredients managing editor Hank Schultz takes a look at what complying with these regulations means for small-tier supplements manufacturers
The dietary supplements industry has long labored under a public perception that its products are unregulated. In the absence of energetic enforcement, an atmosphere was created in which brushes wielded by breathless late-night TV promoters or — gasp! — Smiling Bob could tar an entire industry.
June 25 this year marks a milestone in efforts to put that charge to rest when a promise made in 1994 with the passage of the Dietary Supplement Health and Education Act comes to full fruition. On that date every company, big or small, will have to be in compliance with the Good Manufacturing Practices as mandated by the Food and Drug Administration.
The new regulations add another layer of acronymic verbiage, with GMP joining DSHEA, HACCP, ISO and others. But what does it really mean for the industry?
As with many regulations, it depends on whom you ask. On the plus side, industry insiders say it will add credibility with the public and will level the playing field between ethical players and those inclined to cut corners. On the minus side, some fret about added cost and complexity, and whether complying with the regulations will stifle innovation or even drive deserving companies under.
The GMP rule was first rolled out in draft form by FDA in June 2007 and became final in October of that year. The first deadline in June 2008 for compliance applied to companies with 500 or more employees, followed a year later by companies with 21 to 499.
FDA officials began inspections of larger-sized companies in 2008, and the number of inspections is increasing every year. The agency completed 12 inspections in fiscal year 2008, 28 in fiscal year 2009, and is doing many more now.
So it could be quite a while after June 25 before companies with 20 or fewer employees might actually see an inspector. But it would illegal — not to mention foolish — for a company not to be in full compliance by that date.
As D-day approaches, a preliminary review of what inspectors have found so far gives small-tier companies a glimpse of what to expect.
What to expect
Paper. Inspectors are going to want to see lots of it, in the form of master manufacturing plans, standard operating procedures, and records of all sorts.
"White mounds of paper," said Daniel Fabricant, scientific affairs vice president for the Natural Products Association. "If you don't write it down, it didn't happen."
"FDA takes a risk-approached approach. What are the areas of risk right now for FDA? Let's look at (contamination), and that the products are made as they are written up to be made, and that there aren't accidental overages that could potentially raise a red flag," he said.
Amy Caplette, a group leader at Nutrilite Labs in Lakeview, Calif., who spearheaded that company's GMP compliance effort, said inspectors are looking to see if information in the form of documentation flows through your facility along with your raw materials.
"Most auditors want to see things from beginning to end, from the receipt of the raw material to the shipping of the finished product," she said.
Inspectors will want to be assured that the documents that control that process are easily available to line workers. They will seek to verify that everyone is on the same page, both figuratively and literally.
"How do you control that document?" Caplette said. "Is there a revision number? Is there a date to it?"
"That's one of the biggest traps you see companies fall into; they write SOPs and then don't follow them," said Wes Seigner, an attorney with Hyman, Phelps and McNamara, an FDA/FTC specialty law firm in the Washington, DC area.
No one argues that this newly required level of documentation will add complexity and cost. But it is an achievable and necessary step, industry insiders have said.
"Whatever your documentation is, it is finite. It has a beginning, a middle and an end," said Michael McGuffin, president of the American Herbal Products Association (AHPA). "Whatever (the documentation requirements are), you can get there. Once you're there, it's more of a headache than an obstacle."
Testing — how to do it right
The documents control not only how a company makes a product, but what they make it with. Which brings us to the thorny issue of testing. What constitutes a "scientifically valid" method for verifying the identity of a raw material?
The regulations are loosely defined in this area. Some in the industry say not having fixed standards leaves too much up to individual interpretation, raising the risk of failure. Others laud the flexibility the rule's preamble provides, as it recognizes that there are potentially thousands of different compounds covered by the rule.
"I like 'scientifically valid' because it does leave you and your testing as the master of how you make these decisions," Fabricant said. "If you can show that one identity test is appropriate for your material and you have data to support that, I think that's really the spirit of the rule.
"There's not a one size fits and there's not going to be. I think FDA recognized that there's a lot they don't understand."
A number of different approaches to identity testing exist, from organoleptic analysis for whole substances up to technically demanding forms like HPTLC testing. Whatever method a manufacturer (or supplier) chooses, it has to have good reasons for doing so, and have in place written procedures that will provide a sound and defensible statistical underpinning.
"\[Your testing method\] can't just pop out of a magic hat. You have to have some basis for arriving at the method," said Brien Quirk of Draco Natural Products.
Why you will fail
So you've got your procedures written, your people are trained in their use and you've chosen your testing method and you've got the data to back it up. What can you expect when the inspectors arrive?
You can expect to fail. Almost everyone can expect to get a 483 detailing shortcomings found by FDA inspectors.
"It's very, very rare for inspectors to come into a facility and spend six to ten days there and say, 'Gee, that was perfect,'" McGuffin said.
"We don't see the fact that companies are likely to receive a 483 as evidence of failure. The failure would be if you can't fix what's on the 483," he said.
There is no formal requirement that a company respond in writing to actions it takes to correct 483 issues. But McGuffin, Fabricant and others say a company would be foolish not to document when has been done and promptly forward a copy to FDA.
"It's better to give the agency the info they need to close the file, rather than keep the file open," McGuffin said.
The bottom line
"I think the shakeout is going to be positive. I think it will lead to more consumer confidence," Fabricant said. "As some folks fall by the wayside, I think it will be for reasons of commitment more than anything. I don't think the rule is impossible to meet."
Among the failures in commitment would be failure to rise even to the bar of basic food GMP requirements, which have been in place for years. According to FDA, inspectors already have found a disconcerting number of basic sanitation and pest control issues in looking at big and medium-tier companies.
Along with the shakeout in firms, there will likely be one in products, too. It remains to be seen how much of the cost of GMP compliance that consumers will be willing to bear.
"Once everybody is in compliance, does the retail cost of dietary supplements go up? I can't answer that. We will just have to watch the market," McGuffin said.
About the Author(s)
You May Also Like